Bottling monobloc 6.6.1 with screw capper
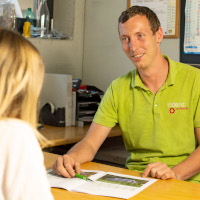
-
Full automatic monobloc filling unit with rinser, filler and ROPP capper
Rinser:
The rinser is used when filling a new glass bottle to remove particles such as dust, condensation water, small insects, etc. The utilization of a rinser gives the bottling plant additional product safety.
With the appropriate options, it is also possible to achieve internal sterilization with a bacteria-killing liquid.
The bottle is gripped securely by the gripper at the bottleneck and then quickly turned upside down by the twist system. The treatment agent (sterile water, ozonized water, air, inert gas, aqueous cleaning solution, etc.) is then injected into the bottle via a nozzle. After an appropriate dripping time, the bottle is turned back moved back on the conveyor. “No bottle-no spray”-system. If there is no bottle in gripper the nozzle is not spaying.
Optionally it is possible to install a two-step rinser system. For example, cleaning fluid and then blow out with air or inert gas.
The cleaning liquid can optionally run through a recycling system. The cleaning solution is collected and pumped through a microfilter and then used again in recirculating.Filling Valves:
The 1000 times proven filling valves of the E2 series can work with gravity (drop pressure) as well as under negative pressure (light vacuum).
Filling under slight negative pressure (optional) on the one hand causes a better release of the filling and on the other hand, it is helpful with slightly foaming products and prevents dripping on the filling valve with worn-out seals.
The height of the bottle is adjusted by handwheel (manual) or can also be done electrical (optionally).
The filling height is set through appropriate spacers which are used in the filling valves.
Pneumatic lifting of the bottle plate and mechanical lowering via cam (no air consumption).
The tub has a central liquid inlet and is mirror polished inside. Total discharge drain with ball valve installed on the bottom of the tank. The opening of the filling valves for sterilization (for example with steam) or for cleaning takes is achieved by stainless steel clips.
Filling valves are easy to remove and can be completely disassembled easily.
Optionally available are two models of cleaning adapters that are used for final cleaning. A cleaning water collection trough is installed under the filling valves or in an alternative a cleaning rim with dummy bottles which allows to collect the cleaning solution under the valves and wash the valves also in countercurrent (backwash).
The liquid feed into the filler tank is controlled via sensors. The sensors will command the pneumatically operated product supply valve and pump control.Other options: hot-filling equipment, high-vacuum, or light-pressure filling. Device for foam extraction.
Capper for ROPP aluminum screw caps
The capsule magazine is mounted on a vibrator base with speed adjustment. As a result of the vibrations, the aluminum screw caps run over a rail upwards and are oriented at the same time. From the tub, the capsules are inserted into the caps distribution channel and then simply taken by the bottle (in flight).
When processing long caps small air piston is available (option) which pushes the capsules on the bottleneck quite down. The height adjustment of the capper is done manually via a handwheel and can optionally be done electrically. Due to the central height adjustment of the screw head is adjusted together with the capsule distributor.
The capper works with a low-maintenance ROPP 4 roll capping head with no cap no roll system. In the caps, channels are installed sensors that control the capsule distributor fully automatically. The machine is prepared for the installation of a capsule elevator.
We differentiate between the pneumatic capper (standard) and a mechanical variant (optional).
In the pneumatic version, the bottles are lifted pneumatically and pressed into the closing head. Recommended for slower running lines.
Optionally, inert gas injection can be installed on caps distribution.The frame of the monobloc is made of stainless steel. All doors are equipped with safety devices in the hinge. The control of the monoblock is carried out via a central control cabinet made of stainless steel. The system is easy and clear to use and also the format change can be accomplished quickly.
Thanks to the modular design and the wide range of additional options, the machine can be optimally adapted to the needs of the company.The system is supplied with a belt, belt drive, and bottle collection table.
Belt, belt drive, and bottle collection table are available as options. Besides, larger bottle-feeding tables are available Ø600-800-1000 mm, and bottle collecting tables Ø600-800-1000 mm with belt drive at the end of the line. Belt connections between different machines are available on request…Filling Monobloc in linear design with single-head ROPP capper.
Rinser: 6grippers 600-800 bottles
Filler: 6 valves 500-800 bottles
Capper: single head capper with fully automatic capsule sorter, distributor, and 4 rolls ROPP head. Capper with pneumatic cylinder lift max. 1800 bottles/h.